
En abril de 2022, las instalaciones insignia de Taylor Farms en Salinas, California, sufrieron un devastador incendio en el lugar donde se encontraban sus principales instalaciones de producción de verduras de hoja verde para servicios alimentarios. El fuego comenzó entre las paredes de la estructura, que tenía décadas de antigüedad, y finalmente llegó hasta el tejado, derrumbándolo en llamas y destruyendo los 60.000 pies cuadrados de espacio de procesamiento. La estructura del edificio más grande que rodeaba la zona de producción permaneció prácticamente intacta.
Inmediatamente después, la empresa decidió reconstruir las instalaciones en el mismo terreno. El Consejero Delegado, Bruce Taylor, también puso el listón muy alto con un plazo de un año para terminar el proyecto. Mientras tanto, las entregas a los clientes de lechuga triple lavada, romana, repollo, espinaca baby, mezcla de primavera baby y hoja verde continuarían según lo programado, aprovechando la red de plantas y distribución de la empresa para hacer frente a las dificultades, confiando en una instalación estacional en Yuma, Arizona, y otras instalaciones locales cerca de Salinas, California, para el procesamiento y envío.
Justo a tiempo, Taylor Farms reabrirá en abril de 2023, pero por el camino la empresa y el socio de diseño/construcción Grupo Dennis se encontró con obstáculos de todo tipo, desde problemas en la cadena de suministro de materiales y componentes hasta fenómenos meteorológicos catastróficos como un río atmosférico que convirtió la obra en un lodazal e inundó también Salinas.

"Esta fábrica fue nuestra primera fábrica en California. Este fue nuestro primer hogar para Taylor Farms, y fue como si la familia se reuniera después de perder su primera casa", dice John Krbechek, vicepresidente de ingeniería de Taylor Farms Foodservice Division. "Fracasar [en la reconstrucción] no era una opción".
En la actualidad, Taylor Farms cuenta con una planta de procesamiento de última generación con un volumen de producción semanal de 15 millones de libras de productos frescos cortados. Se trata de una de las plantas de mayor capacidad del sector y, gracias a su resurgimiento de las cenizas, Taylor Farms ha sido galardonada con el Premio a la Innovación en la Fabricación de la revista Mundo ProFood. Aquí detallaremos cómo Taylor Farms utilizó la pizarra en blanco de la reconstrucción como una oportunidad para aumentar la eficiencia en el procesamiento, la sostenibilidad, el saneamiento y mucho más.
Redistribución de la producción
El triaje estratégico que Taylor Farms puso en marcha tras el incendio comenzó por asegurarse de que los clientes recibían sus pedidos de productos sin interrupción, mientras se creaban planes detallados para reconstruir la planta de Salinas en un plazo de un año.
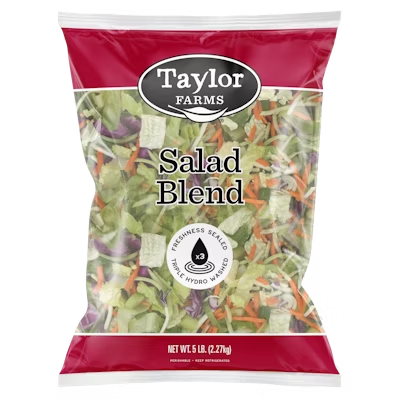
Taylor Farms cuenta con 22 centros de producción en toda Norteamérica y, dependiendo de la ubicación, produce una combinación de verduras frescas y alimentos frescos para restaurantes, escuelas, tiendas de comestibles y tiendas de conveniencia. La planta de Salinas que se incendió se dedicaba al segmento del mercado de servicios alimentarios, por lo que la producción permaneció en la planta hermana de temporada durante un periodo prolongado en Yuma, mientras se creaba un sistema logístico de servicio a los clientes para recibir productos crudos y productos acabados de otros seis frigoríficos.
Cada año, entre abril y noviembre, las verduras de hoja verde se cultivan y procesan en Salinas. De noviembre a abril, el equipo de producción se traslada en camión de Salinas a Yuma para seguir procesando, ya que es entonces cuando se cultivan y cosechan las verduras de hoja verde en esa región.
Por casualidad, como el incendio de Salinas se produjo en abril, todo el equipo necesario para seguir procesando verduras en Yuma seguía allí, a punto de ser enviado de vuelta a Salinas. Así pues, Taylor Farms mantuvo sus operaciones en Yuma, enviando las verduras crudas que ahora se cosechaban en Salinas a Yuma para su procesamiento, y luego de vuelta a Salinas para ser enviadas a los clientes.
Una vez resueltos esos problemas inmediatos de producción, Krbechek y Jeffrey Lewandoski, socio principal de Dennis Group, centraron su atención en reconstruir la planta de Salinas y aprovechar la oportunidad para mejorar y modernizar las instalaciones desde cero.
"Fue bastante devastador cuando miramos [dentro de las ruinas] y todavía estaba ardiendo. Había grandes serpentines evaporativos fundidos en un charco de aluminio. La estructura circundante del edificio sobrevivió al incendio, pero hubo que rehacer, redirigir o reconfigurar la infraestructura eléctrica, de refrigeración, de agua y todos los servicios públicos".
- John Krbechek, Vicepresidente de Ingeniería
Estrategias de saneamiento
Empezar de cero significaba que Taylor Farms podía construir una nueva planta que cumpliera las normas higiénicas más recientes, y que esas normas se aplicaran a todo lo que hubiera dentro. "Toda la instalación es un espacio de lavado higiénico y seguro para los alimentos, incluidas paredes, techos, suelos y desagües; no hay ningún punto que no pueda limpiarse", afirma Lewandoski. "No hay nada pegado a las paredes que no se pueda limpiar por detrás. Tenemos separadores de dos pulgadas en todas las tuberías, conductos, bastidores, y todo está preparado para el lavado, desde las luces hasta las puertas y los marcos, todo puede mojarse, empaparse y desinfectarse", dice, y añade que utilizaron acero inoxidable o acero galvanizado para los materiales porque no se oxidan, lo que puede ser un peligro en una planta alimentaria.
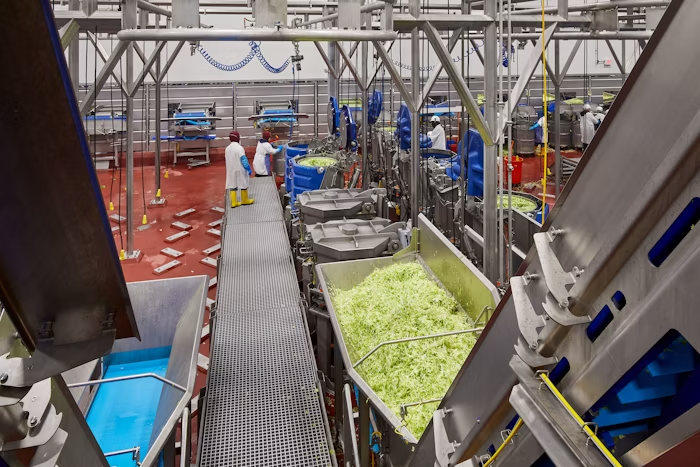
El suelo y los equipos colocados sobre él también se diseñaron con la misma estrategia sanitaria para poder limpiarse desde todos los ángulos. El suelo incluye desagües de zanja y está inclinado estratégicamente en las zonas de mayor uso para evitar la acumulación de agua, algo especialmente importante en una operación de procesamiento de triple lavado. "Todo lo que está en el suelo se mantiene a dos centímetros y medio con almohadillas de lechada.
Nada está apoyado en el suelo, así que todo se puede limpiar", señala Lewandoski. También se mejoraron las zonas de secado convirtiendo los monorraíles aéreos en tubos redondos para que el agua no se acumule en ellos.
Aunque después de cada turno se realiza una limpieza a fondo, Krbechek afirma que al menos una vez al trimestre se desmonta el equipo y se traslada a otra parte del campus de Taylor Farms para limpiarlo a fondo. "De hecho, cocemos [las piezas] en un horno y las horneamos, para que las bacterias no tengan oportunidad de sobrevivir. Nuestra nueva fábrica está diseñada para sacar fácilmente los equipos, limpiarlos y volver a montarlos".