
Em abril de 2022, a principal instalação da Taylor Farms em Salinas, Califórnia, sofreu um incêndio devastador no local onde ficava sua principal unidade de produção de folhas verdes para serviços alimentícios. O fogo começou entre as paredes da estrutura de décadas atrás e acabou chegando ao telhado, que desabou em chamas e destruiu o espaço de processamento de 60.000 pés quadrados. A estrutura maior do prédio que cercava a área de produção permaneceu praticamente intacta.
Imediatamente após o ocorrido, a empresa decidiu reconstruir as instalações no mesmo terreno. O CEO Bruce Taylor também estabeleceu um prazo alto de um ano para concluir o projeto. Enquanto isso, as entregas aos clientes de alface, alface romana, repolho, espinafre, mix de primavera e folhas verdes com lavagem tripla continuariam conforme o programado, aproveitando a rede de fábricas e distribuição da empresa para suprir a demanda, contando com uma instalação sazonal em Yuma, Arizona, e outras instalações locais perto de Salinas, Califórnia, para processamento e envio.
Dentro do prazo, Taylor Farms reaberto em abril de 2023, mas ao longo do caminho a empresa e o parceiro de projeto/construção Grupo Dennis encontrou obstáculos de todos os tipos, desde problemas na cadeia de suprimentos de materiais e componentes até eventos climáticos catastróficos, como um rio atmosférico que transformou o canteiro de obras em um poço de lama e também inundou Salinas.

"Essa fábrica foi a nossa primeira fábrica na Califórnia. Foi a primeira casa da Taylor Farms, e foi como se a família se reunisse depois de perder a primeira casa", diz John Krbechek, vice-presidente de engenharia da Taylor Farms Foodservice Division. "Falhar [na reconstrução] não era uma opção."
Hoje, a Taylor Farms tem uma fábrica de processamento de última geração com um volume de produção semanal de 15 milhões de libras de produtos frescos cortados. É uma das fábricas de maior capacidade de seu tipo no setor e, por causa dessa fênix que ressurge das cinzas, a Taylor Farms recebeu o prêmio Manufacturing Innovation Award da ProFood World. Aqui, detalharemos como a Taylor Farms utilizou a folha em branco da reconstrução como uma oportunidade para aumentar a eficiência no processamento, sustentabilidade, saneamento e muito mais.
Reencaminhamento da produção
A triagem estratégica realizada pela Taylor Farms após o incêndio começou com a garantia de que os clientes recebessem seus pedidos de produtos sem interrupção, enquanto planos detalhados eram criados para reconstruir a fábrica de Salinas em um prazo de um ano.
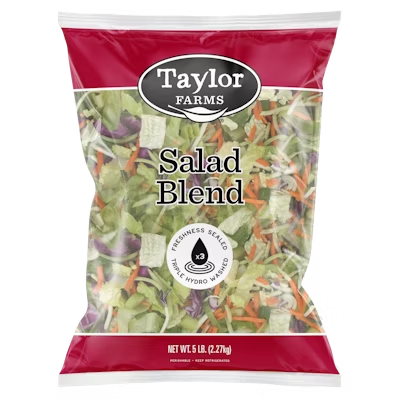
A Taylor Farms tem 22 unidades de produção na América do Norte e, dependendo do local, produz uma combinação de vegetais frescos e itens alimentícios frescos para restaurantes, escolas, mercearias e lojas de conveniência. A fábrica de Salinas que foi incendiada era dedicada ao segmento de mercado de serviços alimentícios, portanto, a produção permaneceu na unidade irmã sazonal por um longo período em Yuma, enquanto um sistema logístico para atender aos clientes foi criado para receber produtos crus e produtos acabados de seis outros refrigeradores.
Todos os anos, entre abril e novembro, as folhas verdes são cultivadas e processadas em Salinas. Depois, de novembro a abril, o equipamento de produção é transportado de Salinas para Yuma para continuar o processamento, pois é nessa época que as folhas verdes são cultivadas e colhidas nessa região.
Por acaso, como o incêndio em Salinas ocorreu em abril, todo o equipamento necessário para continuar processando verduras em Yuma ainda estava lá, prestes a ser enviado de volta para Salinas. Assim, a Taylor Farms manteve as operações em Yuma, enviando verduras cruas que estavam sendo colhidas em Salinas para Yuma para processamento e depois de volta para Salinas para serem enviadas aos clientes.
Com esses problemas imediatos de produção resolvidos, Krbechek e Jeffrey Lewandoski, sócio sênior da Dennis Group, voltaram sua atenção para a reconstrução da fábrica de Salinas e aproveitaram a oportunidade para atualizar e modernizar as instalações desde o início.
"Foi muito devastador quando estávamos olhando [para as ruínas] e ainda estava fumegando. Tínhamos grandes serpentinas evaporativas que simplesmente derreteram em uma piscina de alumínio. A estrutura do prédio ao redor sobreviveu ao incêndio, mas a infraestrutura, a parte elétrica, a refrigeração, a água e todos os serviços públicos tiveram que ser refeitos, redirecionados ou reconfigurados."
- John Krbechek, vice-presidente de engenharia
Estratégias de saneamento
Começar do zero significava que a Taylor Farms poderia construir um novo envelope de fábrica de acordo com os mais recentes padrões de higiene, e esses altos padrões se aplicariam a tudo dentro desse envelope. "Toda a instalação é um espaço de lavagem sanitária e segura para alimentos, incluindo paredes, tetos, pisos e drenos - não há pontos que não possam ser limpos", diz Lewandoski. "Não há nada apertado nas paredes que não possa ser limpo por trás. Temos espaçadores de duas polegadas em todas as tubulações, conduítes, racks e tudo está pronto para ser lavado, desde as luzes até as portas e as molduras, tudo pode ser molhado, encharcado e higienizado", diz ele, acrescentando que eles usaram aço inoxidável ou aço galvanizado para os materiais porque eles não enferrujam, o que pode ser um perigo em uma fábrica de alimentos.
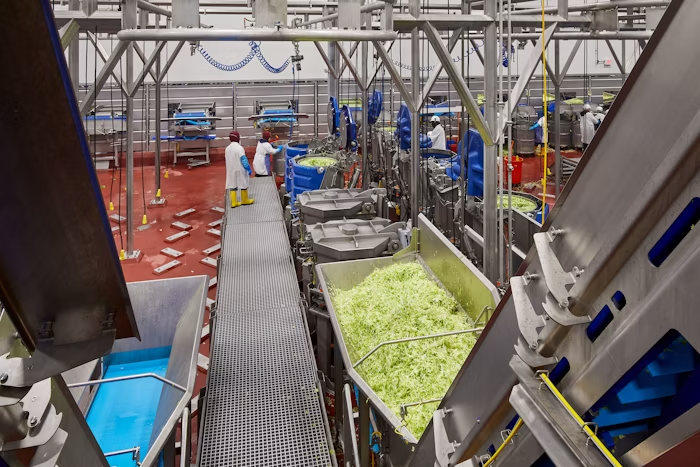
O piso e os equipamentos colocados sobre ele também foram projetados com a mesma estratégia sanitária para serem limpos de todos os ângulos. O piso inclui drenos de trincheira e é estrategicamente inclinado em áreas de alto uso para evitar o acúmulo de água, o que é especialmente importante em uma operação de processamento de lavagem tripla. "Tudo o que está no piso é mantido a uma polegada e meia de distância com almofadas de rejunte.
Nada fica no chão, então tudo pode ser limpo", observa Lewandoski. As áreas de secagem também foram aprimoradas com a conversão dos monotrilhos suspensos em tubos redondos para que a água não se acumule neles.
Embora a limpeza e a higienização completas ocorram diariamente após cada turno, Krbechek diz que, pelo menos uma vez por trimestre, o equipamento é desmontado e transferido para outra parte do campus da Taylor Farms para uma limpeza profunda. "Na verdade, nós cozinhamos [as peças] em um forno e as assamos, para que as bactérias não tenham chance de sobreviver. Nossa nova fábrica foi projetada para levar o equipamento para fora das portas com facilidade, limpá-lo e trazê-lo de volta para dentro para remontagem."